Imagine you need a complicated and risky operation to insert an implant into your brain.
The implant has been custom designed for you and printed on the hospital’s 3D printer.
Earlier, your surgeon used a 3D-printed model of your brain to practice the operation.
And she’s printed a precise, sterile surgical tool to use during the procedure.
The future of medicine?
It might seem like science fiction but 3D printing, or additive manufacturing, is on the path to revolutionise medicine.
Proponents say the technology could speed up surgical procedures, produce customised prosthetics and even print human tissue capable of replacing organs. And it comes with some big advantages.
RMIT 3D printing expert Alex Kingsbury says where typical manufacturing might have a batch size of 100,000, 3D printing offers a batch size of one.
That means it’s easy to manufacture a single product designed for a particular patient.
Using 3D printing also means you can throw traditional design rules out the window.
“You might, say, be able to print a structure for an implant that integrates so much better with bone because it’s got a really complex surface,” Alex says.
“And that means that bone can grow into the implant.”
3D printing can also make objects very lightweight.
“If it’s a wearable or if it’s an implantable that makes a big difference to the comfort level of a patient,” Alex says.
Regulatory headache
The technology does have some drawbacks.
3D printing is usually more expensive that traditional techniques (although in some cases it can be cheaper).
And personalised, 3D-printed devices are proving to be a headache for regulators.
Historically, custom-made medical devices haven’t been subject to the same level of scrutiny as mass-produced devices.
That’s because they were considered low risk, or limited in number.
But 3D printing could see an explosion in personalised implants, prompting the Therapeutic Goods Administration to propose a new regulatory scheme for the devices.
It’s also proven challenging to provide the evidence needed for doctors, health funds and patients to adopt the technology.
How can researchers prove an implant is safe and effective in large numbers if each device is created for an individual patient?
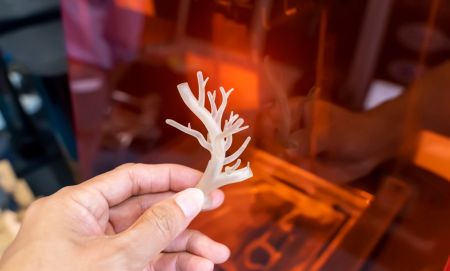
“The frameworks in which we are used to assessing technologies, medical devices, are not frameworks that are actually suitable for 3D printing,” Alex says.
“That’s really down to the customisation element … which makes it quite hard or challenging to standardise information.”
Printing body parts
For Alex, traditional manufacturing produces “dumb products”.
“They’re basic products, they’re designed around traditional manufacturing tools and having some complexity in that product adds enormously to the cost,” she says.
“One of the classic lines about 3D printing is ‘complexity is free’.”
And one of the most exciting developments – the 3D printing of human cells – is still yet to come.
“When we do that, we 3D print the scaffold and we then grow the cells within that scaffold,” Alex says.
“3D printing of cartilage has been done in the lab quite well, and that’s something that everyone is feeling quite confident about now.”
But it’s very much still in the research phase.
“This is technology that’s sitting in universities currently,” Alex says.
“So we’re not going to be walking around with 3D-printed hearts anytime soon.”
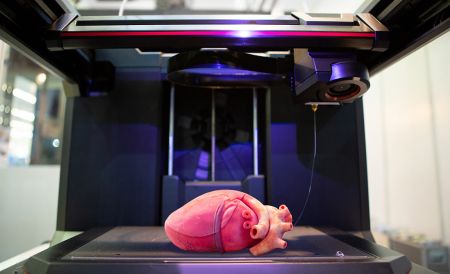